ACEROS ANGELETTI
Horno de Arco
- CONSTRUCCIÓN
- MONTAJE
- INSTALACIÓN ELÉCTRICA
Se llevó a cabo la ingeniería de proyecto, el diseño, la construcción el montaje, la instalación eléctrica y la totalidad de los tableros de un horno de arco de 25 Tn. el más grande construido y funcionando en Latinoamérica, estableciendo a Branch Ingeniería dentro del mercado latinoamericano como la primer y única empresa capaz de llevar a cabo un proyecto de esta envergadura, compitiendo de esta manera con empresas europeas de primera línea a nivel internacional.
Se construyó un sistema de control y seguimiento de producción/consumo, computarizado. Fabricamos y montamos la cuba, bóveda, brazos porta electrodos, el sistema de prensa electrodos, todos los sistemas hidráulicos de movimiento, los pupitres de mando, el montaje del transformador con el sistema de enfriamiento correspondiente, torres de enfriamiento,
tanques, intercambiadores de calor, los tableros de mando, y todas las conexiones de barras de cobre y cables a banderas.
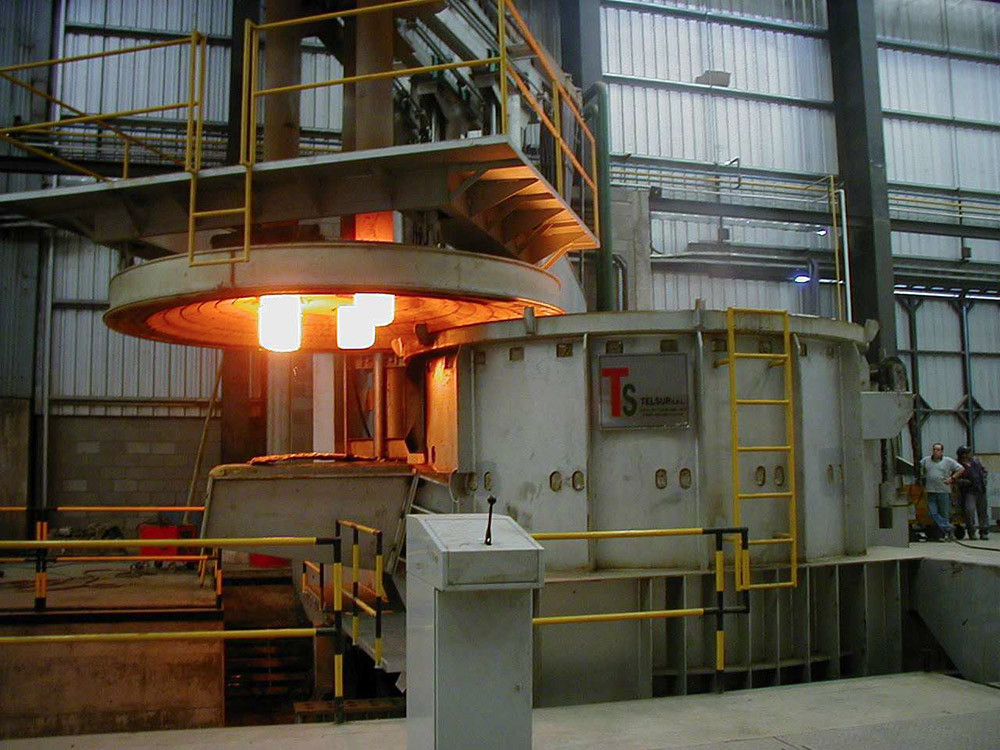
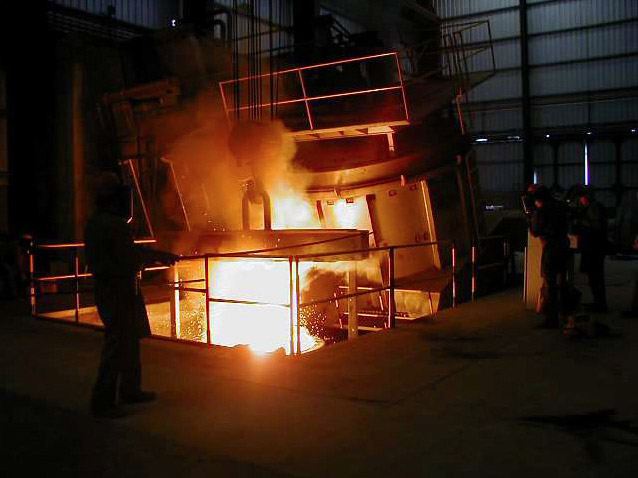
Investigación de mercado: búsqueda en el exterior de trenes de laminación de acero en caliente en desuso.
Aceros Angeletti nos contrata para asistirlos en la visita técnica-evaluativa a AHMSA (Altos Hornos de México) del dúo laminados
– Branch Ingeniería realiza la dirección del desarme, traslado, retroffiting y puesta en marcha en planta Aceros Angeletti, ubicada en el Parque Industrial de Burzaco.
-Branch Ingeniería, junto a Aceros Angeletti elaboró el proyecto definitivo que consiste en la construcción de tres galpones: 26x190 m, 21x110 m y el último de 16x65 m, con la finalidad de instalar en ellos:
- Tren de laminación de lingotes de acero en caliente.
- Hornos de precalentamiento de lingotes.
- Sierra de corte en caliente.
- Enderezadora de barras.
- Sala de transformadores.
- Sala de electrónica.
- Sector de estiba de material.
- Playa de maniobras de camiones.
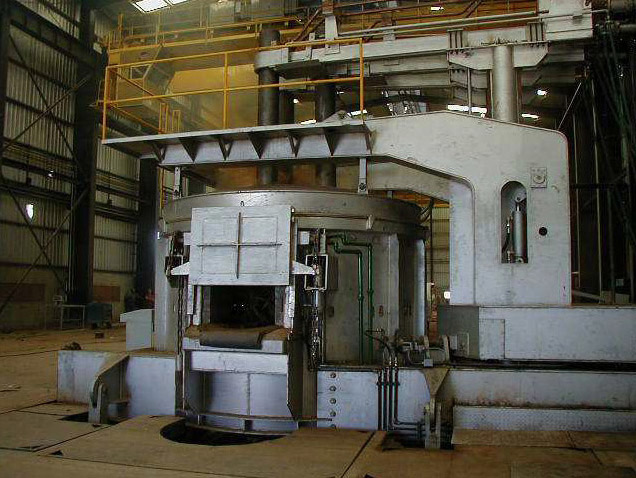
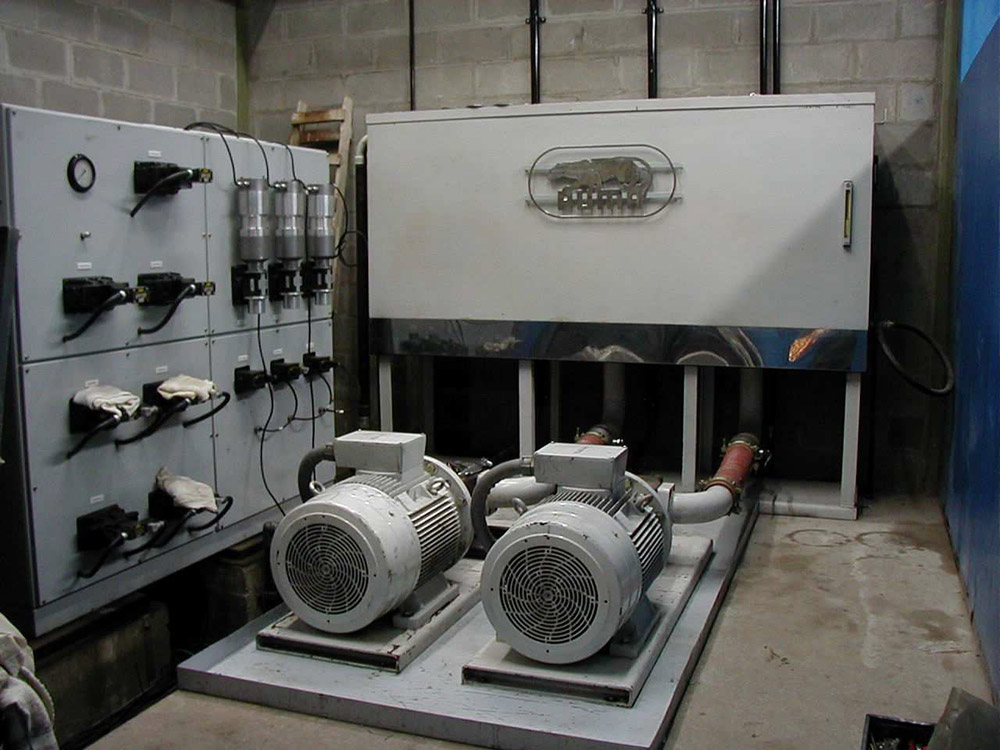
El trabajo fue realizado en 16 meses.
La totalidad del montaje con el reacondicionamiento de todos los equipos, fabricación de estructuras, cañerías, chimeneas, modernización de equipos y software, incorporación de PLC de mandos.
– Branch, realizó la dirección de desarme en la planta de México, con personal propio y personal sub-contratado en el país de origen del equipo.
– Diagramó y llevó a cabo la gestión de importación hacia Argentina, que consistió en el envío de más de 90 contenedores de 40 pies,
– Paralelamente al desarme del Tren de laminación en México, personal de Branch, viaja a EEUU y a Rusia en la búsqueda de equipos para consolidar el proyecto.
-Adquisición de las estructuras para los galpones, puentes grúa y la sierra de corte en caliente en EEUU, y compra de una enderezadora de barrasen Rusia.
– Branch se encarga de realizar el desarme, traslado, mantenimiento y puesta en marcha de dichos equipos desde sus países de origen a planta Aceros Angeletti Burzaco.
– Montaje de los galpones y obra civil que soportaría los equipos.
– Montaje de los puentes grúa, reacondicionados en su totalidad, parte mecánica, parte eléctrica y comandos. Alineación, recambio de rodamientos, engrase, etc.
– Se reacondicionaron y montaron siete (7) Puentes grúa en las distintas naves.
-Un puente de 50:10 Tn., dos puentes de 40 Tn., con cabina de mando y uno de ellos con pinza para lingotes, dos de veinte (20) Tn. y dos de quince (15) Tn.
– Reacondicionamiento de los equipos importados. Se montaron y alinearon mesas de entrada, mesas de salida, la torre de castillo conteniendo los cilindros principales de laminador, se montaron los motores de 3000 HP, con su respectiva transmisión, se fabricó nuevamente toda la línea de engrase a rodillos y cilindros principales.
– Se modificó, reacondicionó y montó la sierra de corte de lingotes, con su respectiva mesa de salida y guía para las distintas medidas de corte, se automatizó totalmente para ser comandada desde una cabina elevada.
– Se realizó el montaje de dos torres de enfriamiento, construcción de cañerías de agua en 4″, 6″, 8″ y 10″. Se construyeron más de 2000 m de cañería de aceite, más de 4000 m de cañerías de servicios, agua, aire, gas, oxigeno.
– Se construyeron 6 hornos de calentamiento de lingotes de tipo “solera móvil”, con quemadores de alta velocidad con sus correspondientes sistemas de encendido y seguridad automáticos.
– Se realizó la construcción y montaje de chimeneas para salida de humo de los hornos de 22 m de largo x 2 m de diámetro y 14 m x 1,5 m.
-Modernización del sistema de mandos del tren de laminación mediante la incorporación de un sistema de control de posición de cilindros de laminación en un tren de laminación Blooming marca UNITED de 2 x 3000 HP con la Instalación de motores de eje con encoders de posición.
– Se instaló el driver de mando en lazo cerrado de posición con censores.
– Instalación de PLC con programas para que automáticamente el operador cargue los lingotes de entrada y producto de salida y seleccione las pasadas en cantidad y regulación.
– Instalación de computadora de mando y visualización.
Otros trabajos realizados
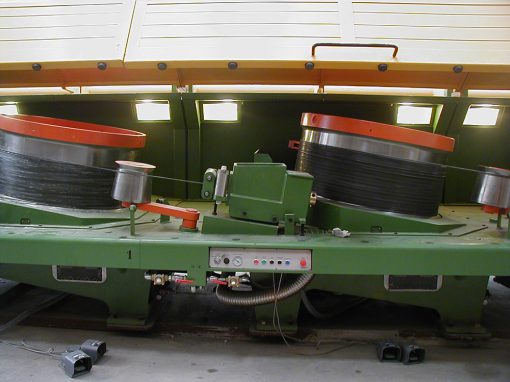
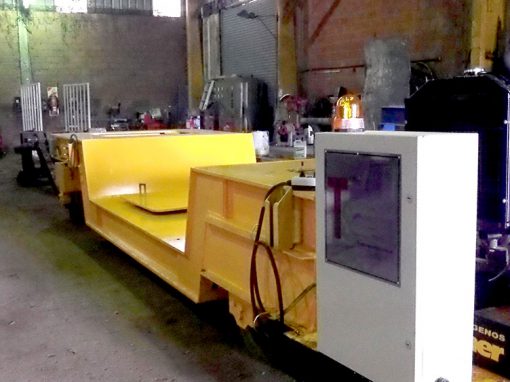
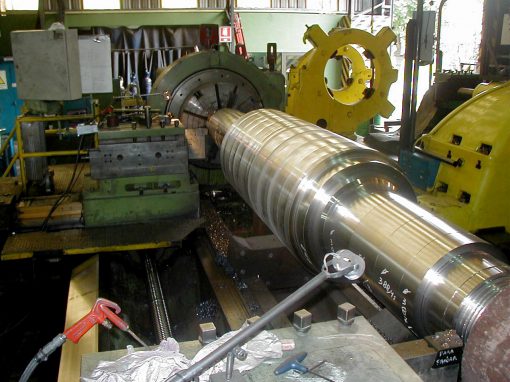
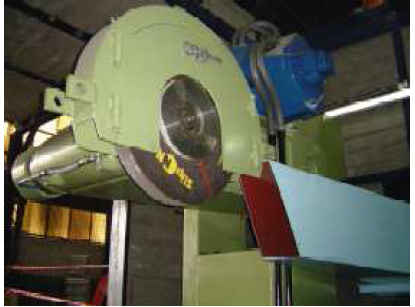
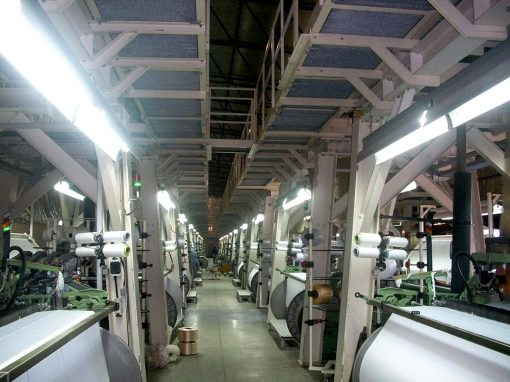
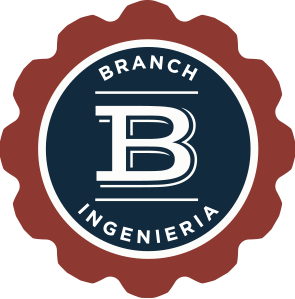
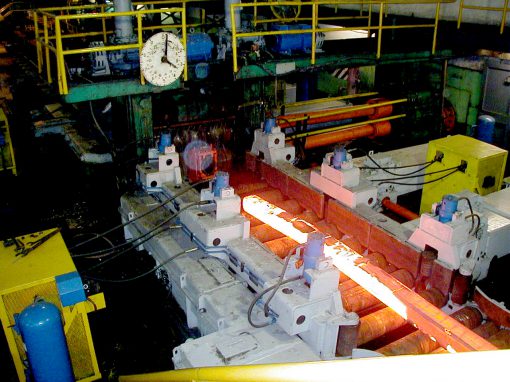
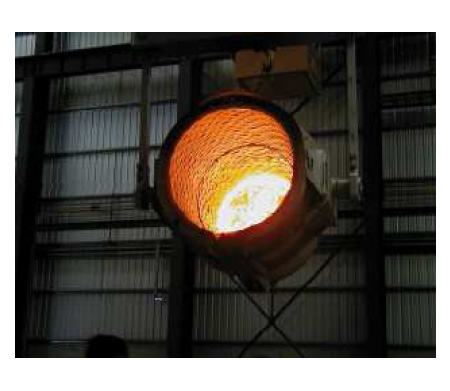
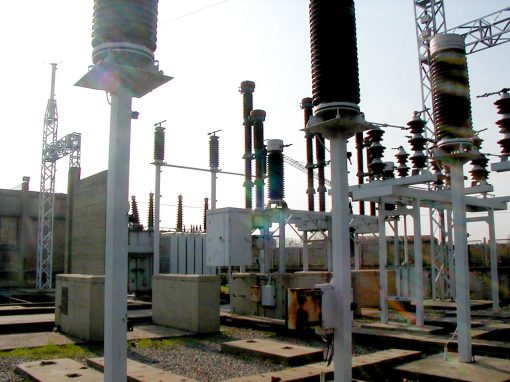
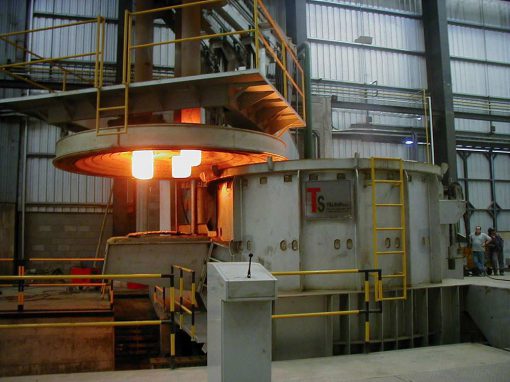